PCA Articles
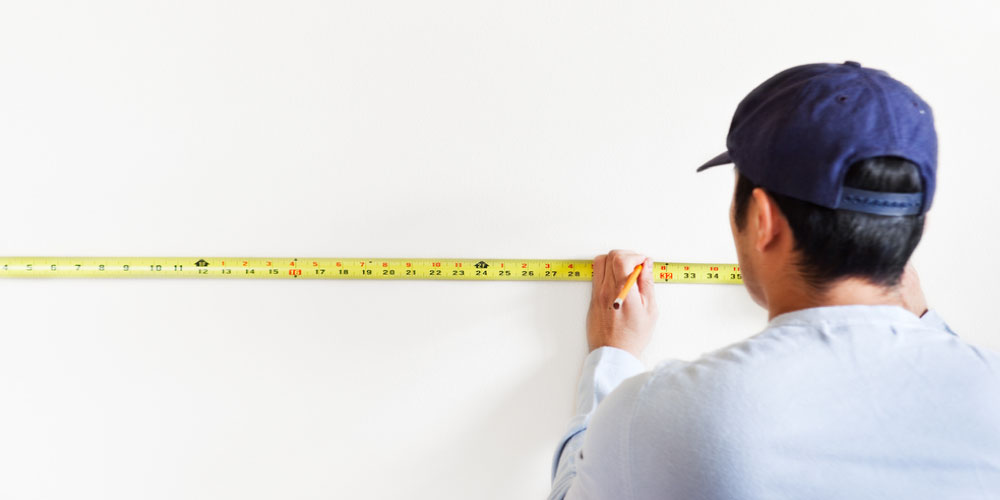
10 Tips For Estimating
Estimates are one of the most important tools to help you land the next job. During one of our webinar series on estimating, Fred Yarur of PEP (Painter’s Estimating Program) outlined 10 foundational principles to support effective estimating procedures.
- Use estimate tools. These enhance your ability to make informed decisions. Estimating is the process of applying past history to predict the costs of future work.
- Measure every surface and count every item. Avoid estimating based on the floor square footage or typical labor rates. Instead, focus on identifying the unique characteristics of the job.
- Use the developed area method. This will help you to produce consistent and repeatable results.
- Make labor assumptions. Assume anything measured is at least 1 linear foot or at least 1 square foot per linear foot.
- Include surface space. Don’t deduct surface space for doorways and openings in walls unless those openings are at least 100 square feet or span floor to ceiling, exceeding five feet in width.
- Account for difficulty. When measuring items that turn at sharp angles, like the sides of door trim, square tubing, or I beams, each adjacent surface should be considered a minimum of half a square foot per linear foot. This process will allow you to increase the actual square footage and allow for these challenges.
- Include all of your time. Remember that the tables of production rates do not include any preparation, setup, or clean up time within a non-preparation type production rate. Make sure you account for that time and estimate it separately.
- Track your production. Use the tables of production rates in volume 2 of the cost and estimating guide if you don’t have your own historical information to use. Be sure to record your own production rates to improve your estimating process in the future.
- Become familiar with MasterFormat. It is the basis for how information in construction
documents are typically organized. - Comb through the blueprints. Treat a set of blueprints or drawings like a detective case and search for surfaces or items that might be within the scope of work. You won’t just find all of the information in one section of the blueprint. You’ll have to look everywhere and carefully read all of the notes.
Want to hear more? Members can check out the webinar series by logging in to their account below. Not a member, join PCA to gain full access to these benefits and more.
Already a member? Login here to see full details.